Direct Current Plasma
Plasma spray processing grew out of earlier thermal spraying methods including electric arc processes and oxy-acetylene flame processes. A coating material, generally in the form of a powder, is injected into a plasma jet during spraying. The high temperature, high velocity jet rapidly heats, melts and projects the powder onto a prepared substrate. At the substrate surface, molten droplets spread and solidify, building up the layers of a coating splat by splat.
The plasma jet is generated by striking a direct current (dc) electric arc between two electrodes within the torch. Gas flowing between the electrodes can be heated up to temperatures of 6,000 K to 10,000 K. The electric arc partially ionizes the gas, hence the term "plasma."
Plasma spraying is a uniquely flexible process, which allows the application of a wide range of materials from plastics to refractory metals and ceramics. It is important to note that the process flexibility permits the deposition of mixed ceramic-metal or metal-polymer coatings.
Because of its high energy and temperature range, plasma spraying has been used primarily for the application of materials with high melting points. These materials are often characterized by a high bonding energy in their crystal lattice and consequently higher mechanical and functional properties such as hardness and chemical resistance. For this reason, these coatings have found use in numerous industry applications (chemical, energy, aerospace, automotive, etc.), where a hostile environment dictates special requirements for equipment.
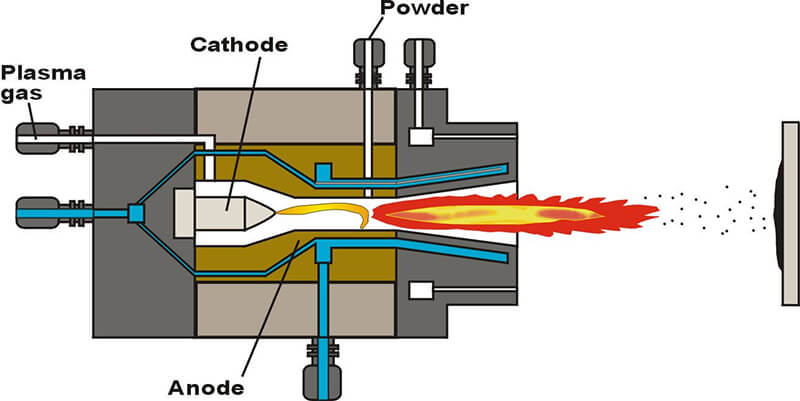