Droplet Impact Experiments
Low Velocity Droplet Impact Experiments
Our research into the impact and spreading of molten metal droplets on a solid surface is part of a larger study of thermal spray coating. This is an industrial process in which metal or ceramic powders are injected into a high temperature gas jet produced by either striking an electric arc or burning a fuel, where they melt while being accelerated towards the surface to be coated. Molten droplets rapidly solidify when they impact on the substrate, producing dense deposits with fine-grained, homogeneous microstructures. Thermal sprayed coatings are widely used to protect components exposed to corrosion, wear or heat. The mechanical properties of coatings are known to depend strongly on the shape of splats formed by individual droplets as they impact and freeze. An understanding of the fundamental physical principles governing droplet impact and solidification is essential to determining the relation between process parameters (such as gas velocity, gas temperature, substrate temperature, substrate thermophysical properties, powder size, and powder material) and the structure of coatings.

Impact of molten tin droplets with velocity 2.0 m/s on a stainless steel surface at temperature a) 25°C, b) 150°C and c) 240°C.

Impact of a 2.2 mm tin droplet with 2.5 m/s velocity on a previous droplet deposited on a stainless steel surface at 25°C with 2 mm offset.
High Velocity Droplet Impact Experiments
To achieve high impact velocities, it is easier to accelerate the substrate rather than the droplet. One way of doing this is to mount the substrate on the end of a rotating arm. The schematic diagram shows the apparatus we built to capture images of droplet impact by synchronizing the ejection of a droplet from the generator with the position of the moving substrate.
The test surfaces on which droplets impinged were stainless steel coupons mounted on an aluminum plate bolted to the outer rim of a 400 mm diameter aluminum flywheel. A vertical rod inserted through the hub of the flywheel was connected to the shaft of a servo motor that could reach rotational speeds of up to 3500 rpm, giving the test surface linear velocities of up to 80 m/s.

Schematic diagram of apparatus to photograph high velocity droplet impact
Impact of 0.6 mm diameter tin droplets with a velocity of 10 m/s on a stainless steel surface with a surface temperature of 20ºC
Impact and boiling of 0.55 mm diameter water droplets impinging with 30 m/s velocity on a stainless steel surface at temperature Ts. Rows a- e show successive stages of impact.

Schematic of the experimental assembly to photograph plasma particle impact
Photographing plasma particle impact
Fundamental studies of plasma-spray coating processes have found that the temperature of the substrate on which molten droplets impact influences their morphology, size, and extent of splashing. Splat morphology affects coating properties such as porosity, adhesion strength, and microstructure Several investigators have found that, for plasma-sprayed particles, increasing substrate temperature reduced the occurrence of splashing and produced disk-like splats.
Photographing droplets in a plasma spray at different stages during impact gives insight into the dynamics of splat formation on both hot and cold substrates. CACT, in collaboration with the National Research Council of Canada’s Industrial Materials Institute (NRC-IMI) in Boucherville, Quebec, are conducting studies to: use a rapid CCD photograph metal and ceramic particles impacting on solid surfaces; and to use high speed two-color pyrometry to measure the temperature and size evolutions of particles during spreading.

Typical thermal emission signals and images of molybdenum splats at different times after impact on glass held at a) room temperature and b) 400C
Droplet generation
Many engineering applications require the production of small, uniform sized droplets. Droplet generators were first developed as research tools to investigate droplet dynamics, spray cooling and droplet combustion, or to calibrate particle size measuring instruments. They have since found use in many industrial applications such as ink-jet printing, dispensing controlled volumes of pharmaceuticals, and deposition of adhesive or solder droplets on circuit boards. In recent years there has been great interest in droplet based manufacturing techniques for rapid prototype production. Development of all these technologies requires a reliable method of generating droplets on demand. CACT has developed a pneumatic droplet-on-demand generator which works by applying pulses of pressurised gas to liquid contained in a chamber, forcing out droplets through a nozzle in the bottom plate of the generator. A solenoid valve is rapidly opened and closed to create pressure pulses. There are no moving parts in contact with the liquid, making the generator simple to build, sturdy, and easy to adapt to high temperature applications.

Schematic diagram of molten metal droplet generator
Single droplet emerging from droplet generator nozzle
Rapid Prototyping by Droplet Deposition
Rapid prototyping by deposition of droplets is an additive process in which components are manufactured from molten materials in a single operation without the use of a mold or other tooling. Near net shape parts are fabricated by sequentially depositing molten droplets layer by layer. Droplet based manufacturing techniques have been successfully used to make components out of wax, polymers, and ice, which are useful for prototyping or to make patterns for castings. Various commercial versions of this technology, popularly known as 3-D printers, have been available for several years.
A logical next step in rapid prototyping technology would be to make functional metal parts by droplet deposition. However, this has proved to be far more complex than simply adapting existing 3-D printers to produce molten metal droplets. Metals of commercial importance have much higher values of surface tension, melting temperature, latent heat of solidification and thermal conductivity than waxes or polymers, making it much more difficult to make droplets fuse together to form a smooth surface after solidification. CACT has developed techniques to make three-dimensional metal parts by droplet deposition. A pneumatic droplet generator is used to produce droplets, which are deposited on a substrate mounted on a programmable stage. By manipulating the substrate complex shapes can be built up.


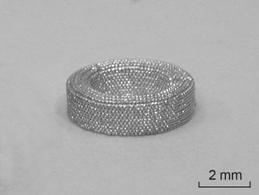
Three-dimensional objects fabricated by depositing 0.18 mm diameter tin droplets